Organic Rankine Cycle (ORC) WHR
ORC WHR & Power Generation
MEEMCO Environment is the representative of the suppliers of (WHR) Waste Heat Recovery Systems integrating the best available (ORC) Organic Rankine Cycle technology into the kilns and furnaces of energy intensive industries.
The Organic Rankine cycle (ORC) is named for its use of an organic, high molecular mass fluid with a liquid-vapor phase change, or boiling point, occurring at a lower temperature than the water-steam phase change. The fluid allows Rankine cycle heat recovery from lower temperature sources such as biomass combustion, industrial waste heat, geothermal heat, solar ponds etc. The low-temperature heat is converted into useful work, that can itself be converted into electricity.

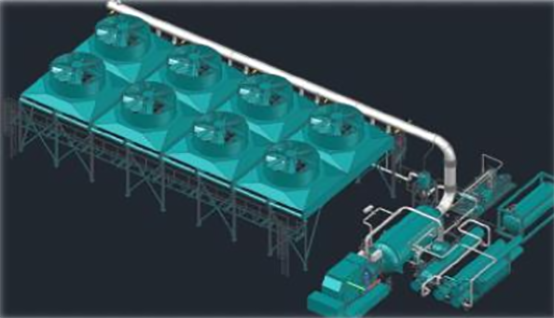
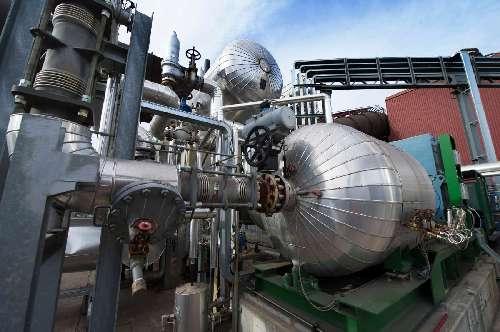
Working principle of the ORC
The working principle of the organic Rankine cycle is the same as that of the Rankine cycle: the working fluid is pumped to a boiler where it is evaporated, passed through an expansion device (turbine or other expander), and then through a condenser heat exchanger where it is finally re-condensed.
In the ideal cycle described by the engine’s theoretical model, the expansion is isentropic and the evaporation and condensation processes are isobaric.
In any real cycle, the presence of irreversibilities lowers the cycle efficiency. Those irreversibilities mainly occur:
During the expansion: Only a part of the energy recoverable from the pressure difference is transformed into useful work. The other part is converted into heat and is lost. The efficiency of the expander is defined by comparison with an isentropic expansion.
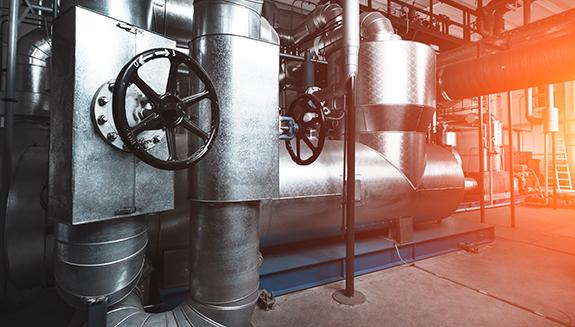
In the heat exchangers: The working fluid takes a long and sinuous path which ensures good heat exchange but causes pressure drops that lower the amount of power recoverable from the cycle. Likewise, the temperature difference between the heat source/sink and the working fluid generates energy destruction and reduces the cycle performance.
Applications for the ORC
The organic Rankine cycle technology has many possible applications, and counts more than 250 identified power plants worldwide.Among them, the most widespread and promising fields are the following:
-
Waste heat recovery
Waste heat recovery is one of the most important development fields for the organic Rankine cycle (ORC). It can be applied to heat and power plants (for example a small scale cogeneration plant on a domestic water heater), or to industrial and farming processes such as organic products fermentation, hot exhausts from ovens or furnaces (e.g. lime and cement kilns), flue-gas condensation, exhaust gases from vehicles, intercooling of a compressor, condenser of a power cycle, etc.
-
Biomass power plant
Biomass is available all over the world and can be used for the production of electricity on small to medium size scaled power plants. The problem of high specific investment costs for machinery such as steam boilers are overcome due to the low working pressures in ORC power plants. Another advantage is the long operational life of the machine due to the characteristics of the working fluid, that unlike steam is non eroding and non corroding for valve seats tubing and turbine blades. The ORC process also helps to overcome the relatively small amount of input fuel available in many regions because an efficient ORC power plant is possible for smaller sized plants.
-
Geothermal Plants
Geothermic heat sources vary in temperature from 50 to 350 °C. The ORC is therefore perfectly adapted for this kind of application. However, it is important to keep in mind that for low-temperature geothermal sources (typically less than 100 °C), the efficiency is very low and depends strongly on heat sink temperature (defined by the ambient temperature).
-
Solar thermal power
The organic Rankine cycle can be used in the solar parabolic trough technology in place of the usual steam Rankine cycle. The ORC allows power generation at lower capacities and with a lower collector temperature, and hence the possibility for low-cost, small scale decentralized CSP units.
For more details of advantages about this technology, please contact us.